Групирането на клиентски поръчки за комисиониране в склада е процес, при който се извършва обединяване на две или повече в поръчки в един лист за изпълнение. Под лист тук ще разбираме набор от складови задачи, които могат да се възложат на един складов оператор.
Най-общо имам два вида групиране – обединяване ( на англ. batch picking) и паралелно събиране (на англ. group picking).
При обединяването количествата от един артикул, който присъства в няколко поръчки се събират. По този начин реално се съкращава броя на задачите за изпълнение, което може да доведе до значително намаляване на необходимото време за подготовка на поръчките . Предимството на този подход е, че мога да се групират голям брой поръчки на различни нива. Може например да се групират всички заявки, които ще се товарят на едно транспортно средство или следва да са готови към определен момент от деня и т.н. При този подход ограничения по отношение на броя артикули и количества се прилага рядко. В зависимост от диапазона на поръчките може да постигнете между 20 и 70% оптимизация. Основен недостатък е, че събраните по този начин заявки следва да се сортират по клиенти или точки на доставка на следващ етап. Ето защо е възможно да загубим част или цялото спестено време при комисионирането, а често дори и да го надвишим. По тази причина е необходимо внимателно да се преценят предимствата и недостатъците на този метод.

При паралелното събиране, заявките се групират, без количествата по артикули да се събират. Всеки артикул се пикира от склада по конкретна поръчка, подобно на конвенционалното комисиониране. Разликата е, че при този вид групиране, складовият оператор събира няколко поръчки в един тур. Обикновено за да се избегнат грешки, като поставяне на артикул в грешна поръчка е необходимо да се предвидят допълнителни контролни процедури. Например при използване на баркод скенер се изисква освен сканиране на артикул и локация, да се сканира и касетка ( кутия ), където се поставя съответната стока. При паралелното събиране има няколко основни моменти, които следва да се вземат в предвид преди да се пристъпи към обединяване на поръчки.
1. Капацитет на средството за събиране на поръчки:
При паралелното събиране е много важно да сме сигурни, че един оператор ще може да събере всички поръчки без да се налага да прави междинни извеждания на стоки до зоните за проверка или експедиция. В противен случай има риск да не постигнем търсеният ефект от съкращаване на времето за придвижване в склада. Самите средства за събиране на поръчки мога да са бокс палети или платформени колички с поставени кутии или кашони. От използваното средство зависи колко поръчки и с какъв обем ще се събират едновременно.
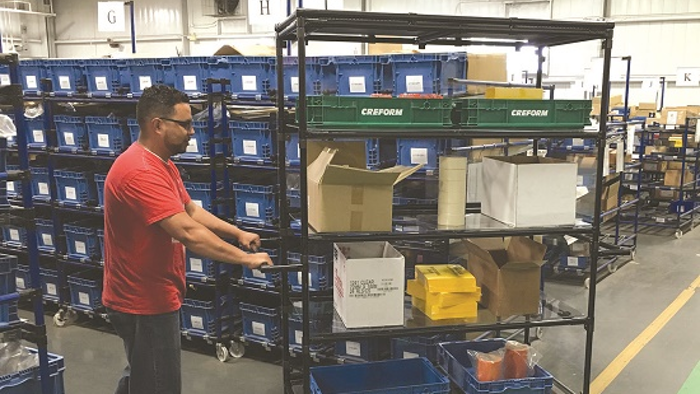
2. Интервал за групиране на поръчки:
От него зависи в каква степен ще успеем да постигнем съкращаване на придвижването в склада. В литературата са известни два подхода: офлайн и онлайн. При първият се групират заявки за изпълнение за следващия ден, постъпвали през целия текущ ден или друг подобен, дълъг период от време. По този начин имаме значително по-голяма свобода за избор на критерии за групиране ( за който ще говорим в следващата точка) и вероятността да постигнем по-добри резултати е значително се повишава. Недостатък е, че ползването на този подход е възможен само ако интервалът за доставка е достатъчно голям (обикновено повече от 24 часа).
При онлайн групирането поръчките се групират или през определен интервал от време или след достигане на определен брой поръчки. В първия случай например, на всеки кръгъл час всички постъпили заявки се обединяват в една или няколко групи ( според зададения капацитет). При вторият подход се определя лимит от брой поръчки ( примерно 20,30), при достигането на който се стартира процедурата за обединяване. Възможно е използването и на комбиниран критерии, съчетаващ първите два, където поръчките се обединяват при достигане на определено количество, но е зададен и максимален период на изчакване, примерно не повече от 2 часа.
3. Критерии за обединяване:
За да постигнем възможно най-добри резултати е много важно да изберем подходящ критерии за групиране. От гледна точка на отчитане на ефекта от групирането в литературата се ползват два основни показателя: изминато разстояние и време за изпълнение на поръчките. На пръв поглед двата критерия изглеждат сходни. Логически можем да допуснем, че при равномерна и непроменлива скорост, при която операторите изминават дадено разстояние, то намаляване на последното ще доведе до съкращаване на времето за изпълнение на дадена поръчка. В действителност обаче при двата подхода, се наблюдават фундаментални различия. Най-важното от тях, е че намаляване на изминатото разстояние със сигурност води до намаляване на времето за изпълнение на поръчките, но обратното не е вярно. Разликата произтича от поставянето на целите, които се преследват при оптимизиране на операциите . Част от изследователите възприемат времето като разход и се стремят да намалят неговата кумулативна величина, докато други се интересуват от времевия диапазон, в който се изпълняват заявките. Втората логика е насочена предимно към нивото на клиентско обслужване и тенденцията от последните години за стриктно спазване на сроковете за доставка. При използване на критерия оптимизиране на разстояние, обикновено се обединяват заявки с близък коефициент на сходство по отношение на траектория на придвижване. Ако си представим например, че имаме две заявки с абсолютно еднакви артикули за събиране, то при тяхното обединяване ще оптимизираме разстоянието за придвижване с 50% - тоест ще изминем цялото разстояние 1 път, а не 2 пъти, както би било при изпълнение на всяка поръчка по отделно. От своя страна моделите разглеждащи времето като критерии за обединяване, включват не само интервала за събиране на поръчките, но и времето необходимо за обединяване на самите поръчки, времето за сортиране и т.н. По този начин всъщност може да се направи много по точна преценка за реалния ефект от обединяването.
4. Алгоритъм за обединяване:
Можем да групираме използваните алгоритми в три основни групи, а именно: Първа Влязла – Първа Обработена ( First Come First Served) ; Пресяващ алгоритъм ( Seed Algorithm) и Оптимизационни алгоритми ( Save Algorithm). Изборът на критерии обикновено зависи от интервала за групиране. Оптимизационните алгоритми дават най-добри резултати сравнение с другите два ( според някои изследвания близо 25%), но за да се постигнат тези резултати са необходими голям брой заявки. От своя страна ПВПО се използва главно, когато интервалът за обединяване е много кратък.
5. Резултати от проведени експерименти
Основна цел на проведените експерименти е да се проучат и оценят възможностите за прилагане на алгоритми за групиране на поръчки с цел повишаване производителността на служителите в компания, дистрибутираща бързооборотни стоки, която от съображения за конфиденциалност ще наричаме условно компания „Х“.
Входни данни и подготовка за провеждане на тестовете
Средната производителност на служителите в компания Х е около 90 задачи на час. Използваният метод за събиране на поръчки е чрез разпечатани стокови разписки. Използват се метод на фиксирани пикинг локации, при който на всеки продукт се задава постоянна позиция.
Средната дължина на една поръчка е 12,34 реда. 74,7% от артикулите в поръчките се събират в количества по-малки от транспортна единица (на единични бройки) и 25.3% се събират на транспортни единици. Артикулите, които се комисионират на бройки се поставят в кашони с цел тяхното опаковане и последващо транспортиране до съответния клиент.
За провеждане на експериментите на сървър е инсталирана система за управление на склад – dsWMS. В склада е осигурена безжична мрежа, която позволява ползване на мобилни терминали с баркод четци, които да комуникират с базата данни на складовия софтуер в реално време. Всички складови локации, от които се събират стоки, са номерирани с баркодове. На произволен принцип са избрани 50 артикула, така че да се обхване цялата площ на склада

Големината на склада е около 1500 кв.м. За съхранение на стоките се ползва конвенционална стелажна система. Поръчките се изпълняват само от количества стоки съхранявани в локации на височина до 2 метра от пода.
Избран е служител от компания „Х“, който да участва в тестовете и на когото е проведено обучение за работа с мобилното приложение на dsWMS. За да се получат лесно сравними резултати, е решено всички тестови поръчки да се изпълнят от един и същи служител, като така се намаляват субективните фактори.
За траектория за придвижване в склада е избран Z метода
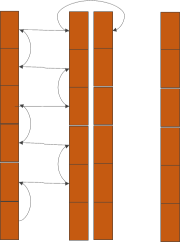
Методика за провеждане на тестовете:
Въз основна на предварителния анализ на данните за структурата на поръчките е допуснато, че възможностите за групиране на поръчки биха се увеличили многократно в случай, че освен по-малки поръчки, отговарящи на критериите, се групират и по-големи поръчки, като първо от последните се отделят артикулите, които са поръчани на цели транспортни опаковки. Тестовете са проведени в продължение на три работни дни с интервал между всеки от тях от два дни.
Артикулите, които ще се събират групово ще се поставят в касетки и ще се придвижват с транспалетни колички. Поради капацитета на основата на палета е предвидено да се комбинират до 4 поръчки в една група
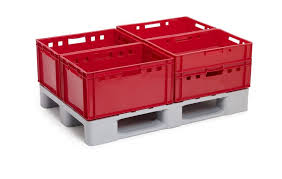
На всяка една касетка се поставя баркод, който се сканира при стартиране на изпълнение на груповите поръчки. При изпълнението на всеки ред от поръчка операторът следва да сканира първо складовата локация, след това баркода на артикула и на последно място да сканира баркода на касетката в която поставя артикула. По този начин се гарантира, че правилният артикул е поставен в правилната касетка и ще бъде доставен на правилния клиент.
За да може да се измери цялото време необходимо за изпълнение на поръчките, всяка от групите се разделя на лотове, които се изпълняват последователно без прекъсване. По този начин чрез записаните данни за първи и последен запис от мобилните терминали се измерва времето за придвижване, време за събиране на артикулите и време за извеждане на поръчките до зоните за експедиция и по-голямата част от времето за подготовка. Не се измерва единствено времето за подготовка на първата поръчка, а при груповите поръчки това се отнася за цялата група, тъй като по време на подготовката не се правят записи в системата.
Изминатото разстояние по време на тестовете се изчислява от системата за управление на склада. Данните, които са въведени за всяка локация са нейното отстояние в метри от началото, края и тунелите в съответния стелажен ред. Между всеки две локации е заложен 1 метър разстояние.
За всеки един от дните за тестване се създават поръчки в няколко групи по следната логика: Първа група с поръчки с кодове, започващи с 1 са т.нар. поръчки за стандартно събиране. Предвидено е тези поръчки да се изпълняват по метода, който стандартно се прилага в компанията, като единствената разлика е че листите са заменени с мобилни терминали. Поръчките съдържат количества от артикули, които са кратни на транспортна опаковка или такива, които следва да се събират на бройка. Втората група поръчки започват с код 2 и те съдържат същите артикули и количества като поръчките от първата група, но само за артикулите, които са поръчани в количества по-малки от транспортна единица. Съответно в третата група са поръчки започващи с код 3 и те сдържат съответно само артикулите от поръчките в група 1, които са поръчани в количества кратни на транспортна опаковка. Тестването на еднакви поръчки при различни сценарии има за цел получените данни да са сравними. По този начин считаме, че се получава пълна съпоставимост на резултатите и се предоставя база за правилни изводи.
През първия ден са въведени общо 24 поръчки – съответно по 8 поръчки във всяка група. Броят на редовете в поръчките в група 1 е общо 101. Съотношението брой артикули които се събират на транспортна опаковка и тези, които се събират на бройка в тестовите поръчки е съответно: 74,2% от общия брой редове е за артикули събирани на бройки и 25,8% на транспортна опаковка – тоест много близко със средното за компанията.
Резултатите от постигнатата производителност през първия ден са обобщени в табл. 1.
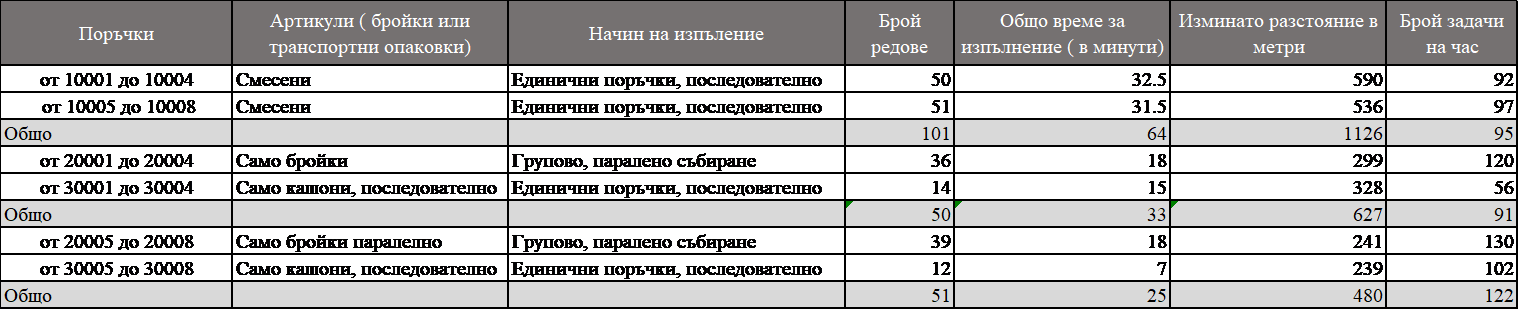
От данните е видно, че при паралелно събиране на поръчки се постига с над 25% по-добра производителност в сравнение с единичното комисиониране, но производителността при комисионирането на транспортните опаковки е много под средното. Това е така, тъй като се изминава значително разстояние в склада за относително малко на брой артикули. При поръчки с кодове от 30001 до 3004 изминатото разстояние за 14 артикула е по-голямо от това за 36. От данните, получени след първия ден на тестване, е видно, че групирането на поръчки води до съществено подобряване на производителността, но отделянето на артикулите, които се комисионират на транспортни опаковки компенсират положителния ефект. Крайният ефект я е, че няма съществено подобряване на производителността от едновременното групирае и последващо разделяне на поръчките.
През втория ден са подготвени общо 15 поръчки, като отново първите 5 са пълни клиентски поръчки, а следващите две групи от по 5 поръчки съдържат съответно само артикулите на бройки или артикулите на транспортни единици. За разлика от първия ден, през втория средният броят документо-редове в поръчка е повишен до 27 реда. Увеличени са и количествата стоки, като по този начин е увеличено съответно теглото и обема. Броят поръчки за паралелно събиране е увеличен до 5. Целта е да се установи как завишените параметри ще се отразят на производителността. Резултатите са обобщение в табл. 2

От проведените тестове през втория ден се потвърждават констатациите от първия ден, че при паралелно групово събиране се постига близо 25% по-добри резултати по отношение на производителността. Другият показател, който прави впечатление е, че увеличаването на броя задачи в една поръчка повишава също оказва положителен ефект върху производителността. Причината за това е, че се съкращава значително средното изминато разстояние за един документо-ред. При смесените поръчки спрямо първи ден то е намаляло от 11 на 5 метра. При груповото събиране показателите са съответно 7,2 метра при тестовете от първия ден срещу 3.47 метра при втория, а при поръчките, в които се събират само транспортни опаковки съответно данните са 21 срещу 10,1 метра.
Същевременно обаче при групираните поръчки е констатирано повреждане на част от опаковките на стоките поради притискане. Операторът изпълняващ тестовете рапортува, че стифирането на артикулите е значително затруднено.
През третия ден са генерирани общо 16 поръчки. Логиката на поръчки, започващи с кодове 1,2 и 3 е аналогична на тази от първите два дни. За този ден са създадени и поръчки с код 4, които са еднакви на поръчките с код 1, но са предвидени за групово изпълнение при паралелно събиране. За да се избегне повреждането на стоки, средният брой редове на поръчка е намален до 18,5 реда, като е въведен и лимит на ниво поръчка до 20 реда на документ.

При анализа на поръчките с код 4 вече ясно се вижда, че групирането води до повишаване на производителността. На база получените резултати тя е в рамките на 23%.
От данните в табл. 1,2 и 3 се налага и един интересен извод, който не е бил цел на проверка, но се откроява при анализа на данните. Ако приемем, че средната скорост на придвижване на един оператор в склада по време на събиране на поръчки е 1 м/с ( около 3,6 км/ч), то можем да заключим, че делът на времето за придвижване при проведените тестове е средно 24%. Той варира в границите от 14% при груповото изпълнение на поръчки с кодове от 20019 до 20023 (табл. 2) и достига до 57% при последователно изпълнените поръчки с кодове от 30005 до 30008 (табл. 3). Според нас този размер зависи както от големината на поръчките ( ако поръчките са по-големи то ще имаме увеличаване на дела на събиране на стоката, спрямо времето за придвижване), така също и от площта на склада ( логично при по-голям склад вероятността артикулите да са по-отдалечени един от друг е по-голяма). Наличието или липсата на подобна зависимост може да се изследва по точно в следващи експерименти. Извеждането на подобни зависимости би помогнало за по-точно прогнозиране на необходимото време за изпълнение на поръчки.